Today is a huge anniversary for me. It is one of the three times in my life that my entire world changed in a heartbeat and oddly enough, in a hugely positive way.
Back in the 1980’s, I was a production craftsman, weaving 30 yard runs of fabric almost every day, sewing the garments cut from that fabric, (with my sister’s help) and spending something like 18 weeks on the road per year setting up for craft fairs all over the northeast, and selling my little heart out. It was a way to make a living, and one I loved for about 8 of the 10 years I did craft fairs. The last couple of years were painful.
I no longer wanted to weave, I no longer wanted to talk to the public, I no longer wanted to explain how long it took to weave/make/etc. I no longer wanted my income tied to the whims of the economy (though that part has never changed and will never change!) I was really really tired.
And I didn’t know how to stop. It was what I did. And craft fairs are booked sometimes more than a year in advance. When do I stop applying? When do I say enough…
Though my husband and I were told we were not able to have kids, way back when we got married, and that was OK with us, I found myself in my mid 30’s completely burnt out, one of the lowest points in my life, and pregnant. Go figure…
So it became obvious that continuing to apply to shows was not in the cards anymore, I did not want to raise a kid schlepping them to fairs, trying to talk to customers and keep them from tearing through the glassmaker’s booth next door. The secret relief of an answer to my exhaustion and burnout, was huge.
And so I was given a way out, the universe was kind, and two kids later, I was able to reinvent myself as a teacher, and a writer, and I found a way.
Except over that next decade, things had a way of creeping back and creating chaos out of my life. I had two school age kids, and multiple teaching jobs locally, plus traveling to teach, plus leading a 4-H group, demonstrating at numerous events, and life had once again spiraled out of control. I did not know how to extricate myself from all of my commitments.
Then came February 22, 2002. I was diagnosed with breast cancer. I was 46, it was aggressive and my entire life came to a screeching halt. There is no better excuse to extricate oneself from life than the “C” word. The secret relief of an answer to my exhaustion and burnout, was huge. All I had to worry about was staying alive. It was all about me and I was allowed to say No. That year of treatment taught me a lot. It taught me what was important and it taught me that I could be creative, and not compromise my soul. I slowly reinvented myself yet again.
And so 19 years later, I’m in the middle of yet another life altering experience, along with the entire rest of the world. For the last decade or so, my life has been mostly on the road. The kids are grown, and teaching nationally required hauling 170 pounds of luggage through all of the nations airports, some huge and sprawling and some the size of a garage. The kind where the ticket agent is also the gate agent and also goes out to bring in the plane when it arrives. I stayed with some of the most interesting people from all over the country, and learned a ton. About life, about how the world is not like NJ, and that’s OK. I learned about different foods, and books and fashion and tastes, and brought back to my own little world a more global experience. I even discovered Scan Pans, Danish cookware that I can’t live without.
But I was tired. I didn’t realize how burned out and exhausted I was. Because venues book sometimes two years in advance, how do I stop? When do I start saying no? In March of last year, I actually spent some time talking to my very patient hostess about this. I was just turning 65. Many of my peers were retiring. I had bookings clear into 2022. How do I say No? How do I stop?
And then the universe provided a way. And this time it was huge. Everything I had booked after that March date in Portland was cancelled. Life as I knew it changed overnight. The secret relief of an answer to my exhaustion and burnout, was huge.
And so this last year has once again, been about reinventing myself. I’m teaching more than ever, yet I don’t have to leave the warmth and comfort of my house. I’m pouring myself into giving back to a community that has supported me for my entire adult life, through the YouTube Channel, The Weaver Sews. I have time to create, to invent, to explore and that is a huge gift for a creative soul. Yesterday I responded to a request to book a retreat, one I’ve done many times and loved, and basically said, I’m done. No more traveling. It was tough to write, but the right thing to do.
And as hard as I’m working, there is time to just create. I’ve been working on a jacket, my 200 jacket pattern, and documenting the construction steps in my YouTube videos. Those include piping, interrupting the piping to make button loops, and stacking buttons when you don’t have anything interesting. And shopping for buttons is out of the question in this time of quarantine. I think that video drops on Friday.
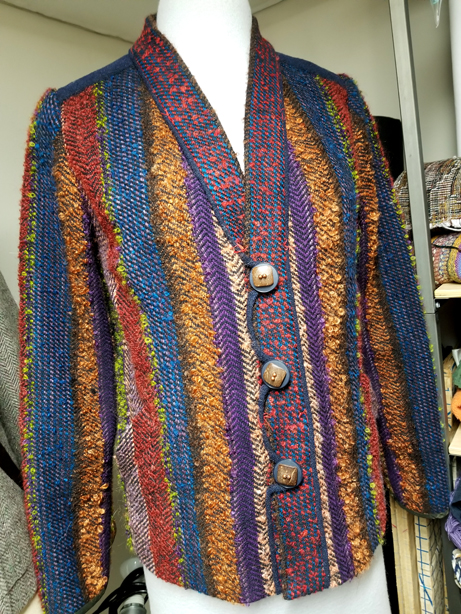
The fabric for this jacket is left over from this coat, it is handdyed and handwoven, in a simple twill pattern. I’ve had fun creating this for the camera. We shot the lining sequence in two parts, and now all I have left is the handwork.
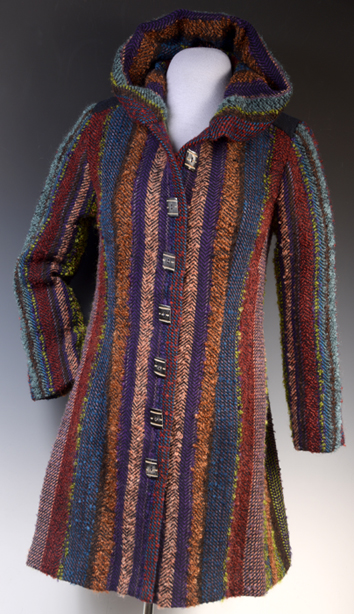
I’ve been teaching a lot this past month, almost daily somewhere in the country, in a couple hours I’ll be teaching in Oregon, and some of the classes I’m teaching have really made me remember back to when/how/why I did many of these techniques. One of the classes especially has made me just want to run to the studio and make stuff every time I give that lecture. That one is called, Leftovers Again? What to do with Leftovers. I sell the lecture as a digital download. There are all sorts of fun techniques I haven’t done in awhile. So this past week, I headed to the sewing studio and just made some stuff.
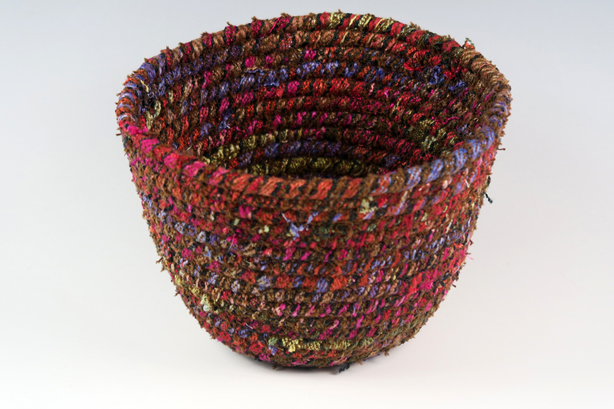
This basket is from coiled scraps of fabric leftover from my handwoven swing coat.
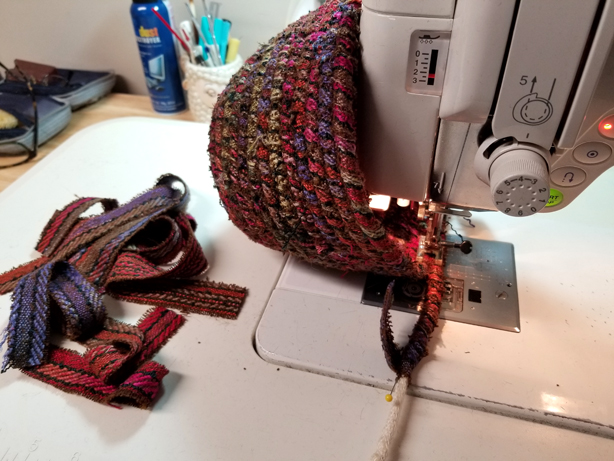
This tote is a pinwheel piecing technique made from scraps from my 1980’s craft fair days.
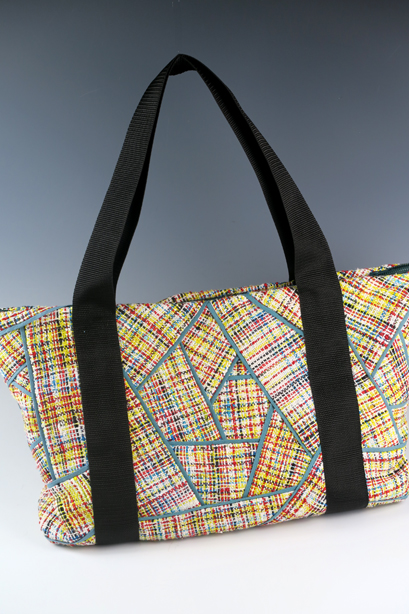
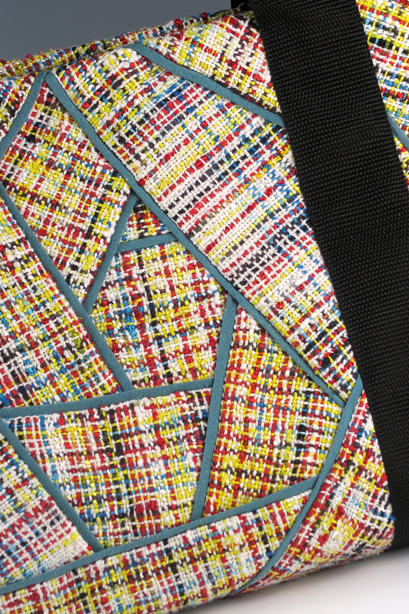
It is snowing again, probably another few inches, but spring is coming. It will be a long time before we see green grass, but I’m OK with that. I spent some time chatting with a friend this morning, about this anniversary day, and what it means when the universe has other ideas about where your life should be heading. She also shares this date, two years ago she was diagnosed with cancer as well. She is still going through treatment. We have a lot to talk about and think about. And celebrate. We survived, so far, and had an opportunity to reinvent ourselves yet again.
Stay tuned dear readers, buckle your seatbelts, put on your masks and hold tight, it is and has been a wild ride, and probably will continue to be…