Of all the places I have taught, Sievers has to be my favorite. There are so many things I love about the experience, just getting there is an adventure, two flights, a two hour car ride from Green Bay Wisconsin, and then a ferry boat ride to a beautiful island off Door County peninsula, into Lake Michigan, to an island that has a powerful hold on all who venture there.
I flew back yesterday, sitting in first class, gotta love those upgrades, happily knitting my socks, completely exhausted, and yet sad to leave such an amazing place. The free margarita in first class helped…
I had another wonderful class, they are all wonderful really, each class I teach presents its own set of challenges and triumphs, but this particular one at Sieve’s has to go down there with my all time favorites. This class in particular is really special to me, I get to teach for four and a half days, which is a really nice chunk of time, so I get to really know the students and help them achieve their goals, and since this is my fourth year teaching this class here at Sievers, I have a number of students who repeat the class each year. Cindy has actually taken this class five times, starting with the Midwest Conference class in Sheboygan, WI I taught in 2005. Nancy and Sherrie have taken the class with me all four years at Sievers, and this is Ginnie’s third time. Terry came back this year for a round two. Others have taken classes with me at other venues and made the trek to Sievers to take my intensive this week.
For those who are taking the class for the first time, I give the agenda, they make a jacket, custom fit to them, from either their handwoven fabric, or if they are a non weaver, whatever commercial fabric they come up with. Silke made this “Daryl” jacket from a commercial fabric electing not to cut into her handwoven on this trip. Nancy is a non weaver, she is actually a jeweler, but she brings the most amazing projects, from fabrics that find their way into her stash, and this year, she brought her grandfather’s WWII army blanket, and made 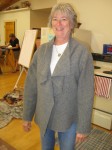
this wonderful jacket from March Tilton’s Vogue pattern 8430. Sherrie worked on a stained glass effect vest from a stack of fabrics she brought.
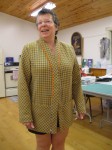
Ginnie made another “Daryl Jacket” from her handwoven fabric, but this time, she lined it and piped it and cut the sleeves and pockets on the bias.
The new students all made jackets that were so personal to them.
Ellen is a really talented quilter, who teaches at Sievers herself, and she used a hand dyed fabric she brought in, along with piping made from one of her quilt fabrics, and Ellen now has a jacket that she can wear with pride and has stretched her sewing machine skills to include garment construction.
Jane made a lovely jacket from her husband’s handwoven fabric. Her husband was along for the ride on this trip, and was a pleasure to have in my lecture on setting and finishing handwoven fabric. And the list goes on. Each student went on a sewing adventure, finding out about their own bodies, how to address fit issues, and how to use their sewing
machines to produce a garment they could be proud of. I manage the flow of the class by instituting a sign up sheet called the “Daryl Alert” and if they need my help, they put their name on the board, and then I go from student to student crossing off each as I go. Only problem was, this class kept me moving so much I’d forget to take a potty break, and some well meaning student (probably Terry) decided to actually put a potty break into the line up for me so I’d remember to go. I love this group!
I’m really big into finishing off the inside of an unlined jacket, and the inside of
Cyndie’s purple corduroy with the Hong Kong seam finishes, made her want to wear the jacket inside out.
Cindy, having been with me the longest, always brings wonderful patterns, and incredible fabrics, and pushes herself to try new things. She brought a fabric she dyed and wove in a class with Heather Winslow 10 years ago at Sievers, it was actually only a sample, which she used on the collar, and then created yardage to match. There is lots of handwork to finish, but Cindy’s stash of handwoven jackets is starting to rival mine.
There were some fit challenges in this class, which helps me grow as a teacher, I love being able to give someone a pattern who can’t walk into a store and buy a ready to wear garment, and have them be able to make a jacket they too can wear proudly. There is just never enough time in the short week here to get it all done. I suppose that if we had two weeks, we still wouldn’t get it all done. Many of the students were already talking about next year.
There was another class running simultaneously, in the other studio, a beyond beginning spinning class, led by Deb Jones, owner of the Fiber Garden in Black River Falls, WI. I so wanted to take her class. On Thursday of the week long class, both of our classes made a studio visit to the other class to see what wonderful things they had done and Deb’s class just made me want to dust off my spinning wheels and dive right in, which I completely intend to do once I stop all this traveling for the year. I learned so much just watching all the demonstration stations she set up. I heard nothing but rave reviews from her students.
The weather at Sievers was a bit stormy, and we lost power one night, later in the evening, creating a surreal acknowledgement of how much we rely on electricity. Ann, owner of Sievers, happened to be in our studio at the time and instantly produced flashlights so we could all find a safe comfortable place to sit down, and I took a flashlight and an umbrella and made a made dash for my cottage to bring over my last remaining glass of wine. Well I can’t take it home on the plane with me. Seemed like the perfect thing to do in this situation. Within about fifteen minutes, the generator was turned on for the whole island, and power was restored, and we resumed sewing well into the night.
The views on the island are peaceful, serene, and restorative. As hard as we all worked, there is such a sense of accomplishment and pride, and lots and lots of inspiration to draw from once back on the mainland.
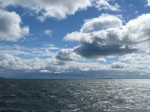
The ferry ride back yesterday was quite the trip, after all the storms the night before, the water was choppy and the spray up over the front of the ferry drenching.
Donna Kallner, one of my all time favorite fiber buddies, we roomed together at that now infamous Sheboygan conference, teaches frequently at Sievers, but this time she was a student taking Deb’s class. Donna and I had a really nice long chat on the two hour drive back to Green Bay and the airport on Friday. She graciously volunteered to drive me, we stopped at a wonderful place for lunch, an old county meeting hall converted to a cafe, the whitefish salad sandwich was to die for!
I’m home now. And so is my husband, who flew in Thursday from Saudi Arabia. My children are also home, if even only for today. We actually all sat at the same table tonight, just the four of us, and had ourselves dinner. It was a really special dinner. It is really good to be home.